GERALD CARDEW SQUARE SECTION SPRINGS
|
|
28-4-94
273
The appearance of the Weihrauch HW97K caused a big flutter in the pigeon loft because it is fitted with a square section spring. Many people, knowing that I have a personal dislike of these springs, got in touch with me on the subject and I immediately decided to look carefully into the subject to see if I could find where the truth really lies.
However, prior to describing my comparison tests of square and round springs I must first put the record straight by mentioning the book “The Airqun from Trigger to Muzzle” which was first published in 1976. In that work we said, “The normal material for springs is manufactured in the form of round wire hardened and tempered ready f or winding into the finished product. It is f or this reason that springs of square section are not readily available. The high quality steel that is drawn into round wire is, we understand, not drawn into square or rectangular section. So, even if one does get hold of such a spring, the chances are that the advantages to be gained from the larger section will be outweighed by the poorer material.” This obviously indicates that we had high hopes of a square spring.
At the time of writing the book we took what appeared to be the commonsense view that if the input power of a spring gun could be increased the output power would obviously increase also. This idea has, in the light of further work, proved to be one of the great fallacies of spring airguns. There is an optimum spring power for any rifle above which the velocity starts to fall back, which is a very hard statement to swallow. However, good quality round section springs have in my experience always proved capable of meeting this optimum figure with ease.
|
|
273 page 2
It has often proved possible to exceed this optimum spring power in certain rifles with “special” springs resulting in increased recoil but with little velocity increase. Many rifles are built with below maximum springs because the reduced recoil of the lower powered unit offers greater accuracy; like everything else in airguns a compromise has to be struck.
My dislike of square springs is founded on experiences when fitting them for clients and also firing other people’s rifles fitted with them. I have always found that the rifles have suffered from excessive recoil and have proved harder to cock, all coupled with a reduced Energy Storage Capacity in the spring. (ESC)
When the HW97 arrived for test I was more than curious to find out how well it worked with its square spring, further more I was determined to exchange the square for a round spring manufactured for a similar rifle. The square section spring had a ESC of 32.1 Ft. Lbs. and produced 10.7 Ft. Lbs. when firing a 14.4 grain pellet. An alternative round section spring had an ESC of 43 Ft. Lbs. and yielded 14 Ft. Lbs. when firing the same pellet. So clearly in that gun the round spring had considerable advantages over its square counterpart.
It is worth while taking a close look at what the commercial spring makers have to say about springs in general, also square springs and their application in industry. The first thing that is very noticeable is the complete absence of any information about airgun springs; this is simply because in a gun they are stressed far beyond anything that would be normally considered acceptable in an industrial application; we in airgunning accept that our springs will not last forever. If we compare the life of one of our springs with that of a car engine valve spring it puts things into perspective. Suppose we get ten thousand shots, or double or even quadruple that number before one of our springs collapses,
|
|
273 page 3
then a valve spring will be expected to survive that number of compressions without trouble during the first few miles up the motorway. Firms who stick their necks out to make springs for us do so on the understanding that their life will be short when compared with similar products bound for industry. So any design factors laid out in commercial literature about square springs must be viewed in the light of an industrial product manufactured for a far less demanding life than we require.
Text books will say that square section springs should be avoided except in instances where their advantages make them a worth while proposition. A square spring has a slight advantage where maximum stiffness is required within a confined space, however even then there will probably be a price, not only in financial terms, to be paid because the operating deflection may have to be limited to avoid over-stressing the spring. The risk of over-stressing is increased because the square material from which the spring is made is not of the same high quality as the round.
The reason for the lower quality of square material is one of economics, there is far less demand for square material so the wire manufacturers neither use the same high quality material nor put the final product through the same refining treatments as they employ for the round material. Of course these statements are founded on information which may now be slightly out of date; if the demand for square springs has increased in recent times, the better quality steel may currently be drawn and processed by the same procedure as the round. However, the square section spring I bought recently as a guinea pig emphasised the statements because although of about the same number of turns, it was far shorter than an equivalent round spring, suggesting that it could not withstand an equal stress.
|
|
273 page 4
The text books go into long winded descriptions of the fact that when square material is wound into a spring the outside edge of the square is stretched and therefore its width is reduced, while at the same time the inside edge is compressed and therefore becomes wider. The total result of this deformation is that the material becomes shaped like a keystone and therefore the coils cannot be compressed as close together as in a round spring. Although this limitation may be a difficulty in some engineering applications, as far as airquns are concerned it is of no consequence because our springs are seldom totally coilbound when the gun is cocked.
However, in the past I have seen square springs in which the material has not been laid down correctly and is slightly cocked over and out of parallel with the centre line of the spring. This error has resulted in one corner of the wire standing above the outside diameter, whilst the diagonally opposite corner reduces the inside diameter of the spring. These two sharp edges act as scrapers and cut material from the inside of the piston and also from the outside of the spring guide as the piston and spring move forward and back along them; the swarf produced then combines with the grease to form an rough compound while the piston and guide are irreparably damaged by the scraping action. Neither the spring I purchased nor the unit fitted to the HW 97K showed any signs of this faults their outside diameters were as smooth as may be expected of this material, though it must be said that the degree of polish was not as good as that on most round wire springs.
The guinea pig square spring (No 1) was bought to fit my HW8O .22. The round section spring (No 2) was a new one I had on stock from the days when I sold English made replacement springs for HW rifles.
The two diagrams used to calculate the ECS of the springs
|
|
273 page 5 are shown. The first two immediate obvious differences are that the angle of the slope of the square spring is much steeper than that of the round spring, this implies that this spring conforms to the text book and is stiffer than its counterpart; the other factor is that the whole figure belonging to the square spring is shifted to the left of the diagram and is also slightly smaller in area, this indicates that it possesses a lower ESC.
Once I had tested the springs I stripped the HW 80 and cleaned out all the old lubricant replacing it with a small amount of the type of grease that was used when the rifle was built. I then fired 14.4 Grain Wasp pellets until I had enough shots to provide a reasonable average velocity for each spring. As so often happens when a rifle’s insides are disturbed and a new spring fitted, there was a tendency to slight dieseling. These shots were ignored and after firing the spring’s length was checked to see if it had become shorter as so often happens when violent diesels occur. These dimensions are listed on page 10.
The square spring produced an average velocity of 658 FPS while the round produced 695 FPS. These velocities calculate out to energies of 13.7 and 15.4 Ft.Lbs. respectively, showing a reduction of 11 percent when using the square spring. The difference between the input energies provided by the springs was virtually the same at 10.3 percent; this is an interesting similarity because in both instances the difference between the output energy of the rifle and its input energy works out very close to 31.4 percent which indicates to me that neither spring was providing the maximum power that the rifle could handle.
Referring back to the HW 97, if the same calculations are carried out for that rifle it will be shown that the square spring’s 32.1 Ft.lbs. produced an overall efficiency of 33.3 percent while the round
|
|
273 page 6 spring s 43 Ft.lbs. gave a slight reduction to 32.5 percent. This would indicate that for maximum efficiency, though not necessarily velocity, an
input energy of about 32 Ft.Lbs. would probably be the best. This is of course a somewhat academic figure since we air gunners are usually after the maximum velocity and are not too bothered by efficiency, and in any case it is highly likely that the efficiency figure will have been boosted by the combustion of a small amount of lubricant.
When cocking the rifle I made a note of the maximum force that was required at the muzzle to cock it, the difference was small, the round spring required 24 Lbs. while the square required 25 Lbs. Even the spring balance had difficulty in indicating the disparity. While firing the rifle I made a mental not of the difference in recoil, or jerk. Again it was difficult to be quite sure which spring produced the greater, but in the end my final judgement came down on the round spring; the rifle had the be held slightly firmer when it was fitted to give a close group.
The two diagrams contain an area which I have marked Z, this area represents an unusable amount of energy always stored by the spring due to the initial compression. In the case of the square spring this will be about 2.3 Ft.lbs. while the round spring will store about 10 Ft.lbs. Although neither of these packets of energy have any direct effect on the power of the rifle since they are unusable, they have a profound indirect effect because their very existence indicates the amount of initial compression applied to the spring before the gun is cocked and therefore influence the size of sections X and Y of the diagram which are the areas indicating the usable stored power available in the cocked spring.
If you imagine that the round spring No.1 is two inches shorter, then its initial compression will be reduced to only half an inch, but since the piston stroke must still be the same at three and a quarter
|
|
273 page 7 inches the whole of area Z will just about disappear, areas X and Y will be shifted to the left and area Y will virtually disappear also, leaving the only energy available that stored in area X. It is for this reason that when a spring becomes shortened through dieseling its ESC goes out through the window.
The size of Z also has an influence on the jerk felt as the rifle is fired. The greater the initial compression the greater will be the force hammering the piston against the cylinder end once the shot has been fired. In this instance the shortness of the square spring was probably responsible for the reduced jerk when that spring was fitted.
It was at his point that I phoned my friends at Manchester Air Guns to check that my guinea pig spring was correct for an HW 80. “Which one have you got,” they asked. That really put a cat amongst the pigeons as far as I was concerned. To cut a long story short they kindly agreed to lend me a further three springs for test, making a total of five possible springs for the same gun three of which were square and two round. It makes me wonder just how many alternative springs there are available for this, or any other rifle. Two swallows don’t make a Summer, now I had three with which to gauge the situation. Subsequently spring 6 arrived from another source.
Testing the three that arrived from MAG using the same procedure as the previous two gave a set of very interesting figures which are now tabulated. It would be tiresome and pointless to draw out the ESC graphs for each spring because this may be done by using the samples as a model, I arrived at the figures by use of a programable calculator.
Inspection of the table reveals many interesting facts. Spring 4 was the longest yet being very “soft” did not have the greatest ESC. No.6 yielded the greatest output and also had the greatest ESC. No.5
|
|
273 page 8 stored a large amount of energy yet did not produce the greatest output power, it must be assumed from the table that the rifle seems capable of handling in excess of 58 Ft. Lbs. No.1 not only stored a surprising amount of energy for its size but also produced a large amount of output power.
So as to make the comparison of these six springs easier I have laid out the slope of their characteristics, while at the same time I have circled the point C which is the starting point for the construction of areas X, Y and Z.
The stored energy was calculated on the “Length after compression” figure even though the length may have been reduced at some time during the actual shooting. Had it been calculated on the “Length after shooting” the result would in most cases have been exactly the same. Spring No.5 lost most length during shooting, this was mainly due to three shots which dieseled heavily, taking the power up to 31 Ft. Lbs. for those three shots only.
The recoil or jerk was in every case compatible with the power of the spring in question, it was certainly greatest in the case of No. 6, but was still just about acceptable, the heavy HW 80 being able to absorb and control the worst of it.
Looking back at what started out as an interesting little exercise to prove something I already knew, the project has grown into a marathon. I must say I now feel better about square section springs; perhaps their manufacture has improved since I last seriously tested one, perhaps as I suggested earlier the quality of the material has in fact been improved. The reduced performance of the square spring in the HW 97 may perhaps have a political or commercial explanation; while the poor performance of the square spring No.2 in my 80 surprised me, it seemed too short for the rifle, it was this lack of length that caused the phone call
|
|
273 page 9 to MAG allowing them to pull the rug from under my feet. Until I made that phone call I had convinced myself that round section springs were still unbeatable. Of course this project has been conducted over a somewhat limited period of time, even though it has taken four times longer than anticipated, the test of the pudding lies in the eating and I have only had time to taste a spoonful of each. The long term life of any spring is a different kettle of fish altogether, as we know manufacturers will only give a “guaranteed for life” certificate with them; but how long is life in the fast lane?
No spring worth its salt will be harmed by leaving the gun cocked for long periods, though of course this is a dangerous practice which should be avoided at all times. Excessive dieseling is the guaranteed technique for reducing a spring’s useful life.
Spring No. 1. Originally made by FSR of Rochdale for sale by CARD. FSR no longer exist.
Spring No.2. An Ox unit bought locally for an HW8O.
Spring No.3. Airforce spring. Supplied by MAG.
spring No.4. Helston Springs. Supplied by MAG.
Spring No.5. HW8O “Export”.Supplied by MAG.
Spring No.6. HW8O “Special” Helical Springs.
Spring No. 6. Is the only spring to have been shot peened. This process removes surface stresses and increases its resistance to failure by fatigue cracks.
|
|
273 page 10
Spring Number | 1 | 2 | 3 | 4 | 5 | 6 |
Type | Rnd. | Sq. | Sq. | Sq. | Rnd. | Rnd. |
Weight of Spring. Ounces. | 5.93 | 6.44 | 5.93 | 5.36 | 6.18 | 5.68 |
Weight of Spring. Grammes. | 168 | 182.5 | 168 | 152 | 175 | 161 |
Length when new. Ins. | 11.20 | 9.37 | 10.95 | 12.87 | 10.73 | 10.87 |
Length after compressing. Ins. | 10.85 | 9.3 | 10.45 | 12.77 | 10.7 | 10.60 |
Outside diameter. Ins. | .915 | .910 | .90 | .860 | .90 | .90 |
Total number of turns. | 33 | 31 | 30 | 38 | 32 | 30 |
Dimension of material. Ins. | .142 | .140 | .135 | .120 | .150 | .150 |
Cross sectional area. Sq.in. | 0.0158 | 0.0196 | 0.018 | 0.0144 | 0.0176 | 0.0176 |
Length at 100 Lbs load. Ins. | 8.46 | 7.62 | 8.58 | 8.80 | 8.63 | 8.78 |
Deflection at 100 Lbs. Ins. | 2.39 | 1.68 | 1.87 | 3.97 | 2.07 | 1.82 |
Length at 200 lbs load. Ins. | 6.20 | 6.08 | 6.70 | 5.20 | 6.85 | 6.95 |
Deflection at 200 Lbs load. Ins. | 4.65 | 3.22 | 3.75 | 7.57 | 3.85 | 3.65 |
Length fully compressed. Ins. | 4.82 | 4.63 | 4.42 | 4.66 | 4.86 | 4.61 |
Length in uncocked gun. Ins. | 8.31 | 8.31 | 8.31 | 8.31 | 8.31 | 8.31 |
Length in cocked gun. Ins. | 5.06 | 5.06 | 5.06 | 5.06 | 5.06 | 5.06 |
Initial compression Point C. | 2.50" | 0.99" | 2.14" | 4.46" | 2.42" | 2.29" |
Piston stroke. Ins. | 3.25 | 3.25 | 3.25 | 3.25 | 3.25 | 3.25 |
Length remaining uncompressed. | .24" | .43" | .64" | .4" | .2" | .45" |
Stored Energy. Ftlbs. | 48.6 | 43.6 | 54.4 | 43.0 | 56.7 | 58.1 |
Output Energy. Ftlbs. | 15.4 | 13.7 | 17.2 | 12.8 | 16.7 | 18.6 |
Length after shooting. Ins. | 10.85 | 9.33 | 10.33 | 12.75 | 10.26 | 10.60 |
Cocking effort 20" barrel. Lbs. | 23 | 25 | 26 | 23 | 30 | 32 |
Efficiency% * | 31.7 | 31.4 | 31.6 | 29.8 | 29.5 | 32 |
* The efficiency figure of pellet power to spring power is only a guideline for comparison since a certain amount of combustion will have taken place, increasing the velocity.
|
|
273 page 11 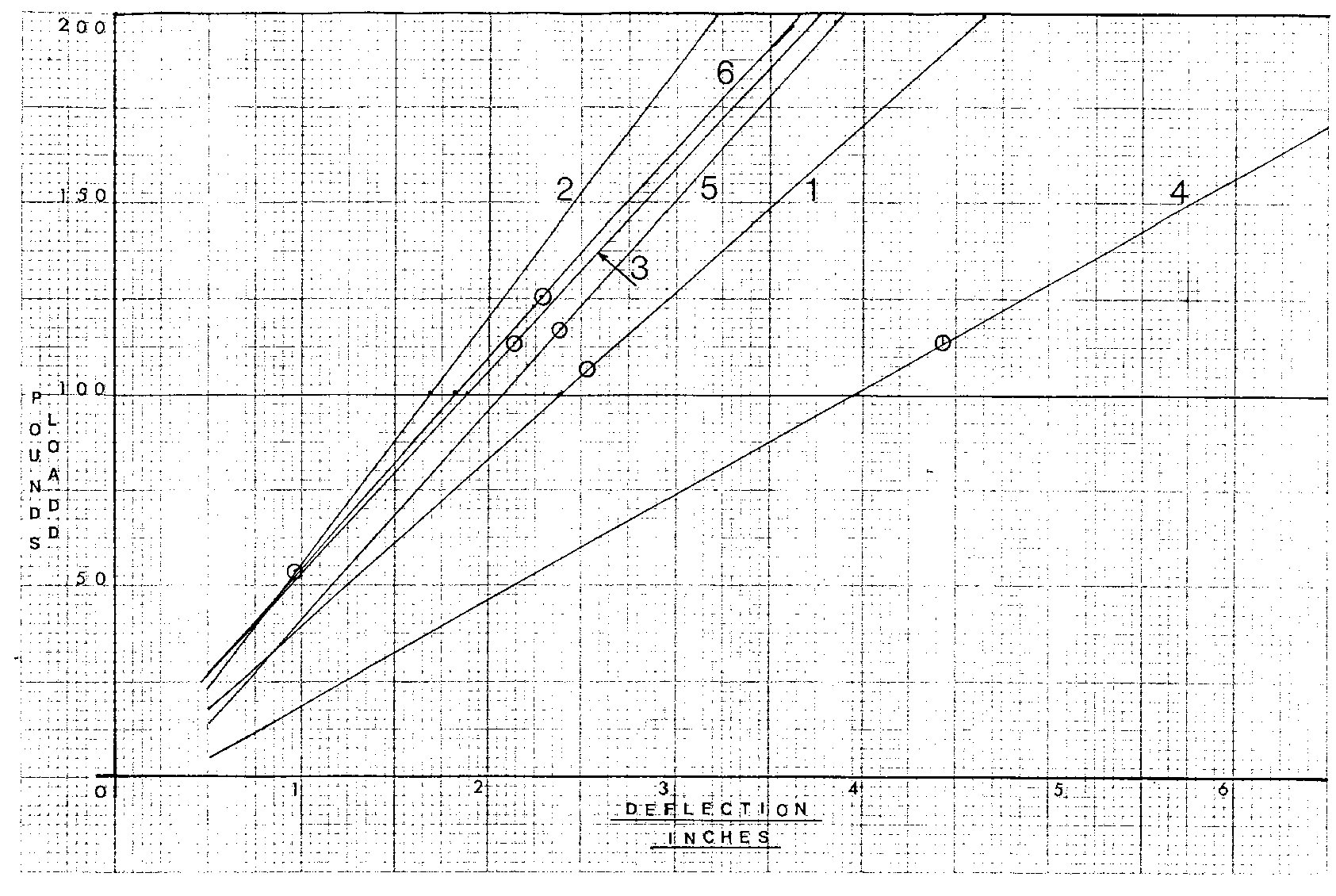
|
|
273 page 12 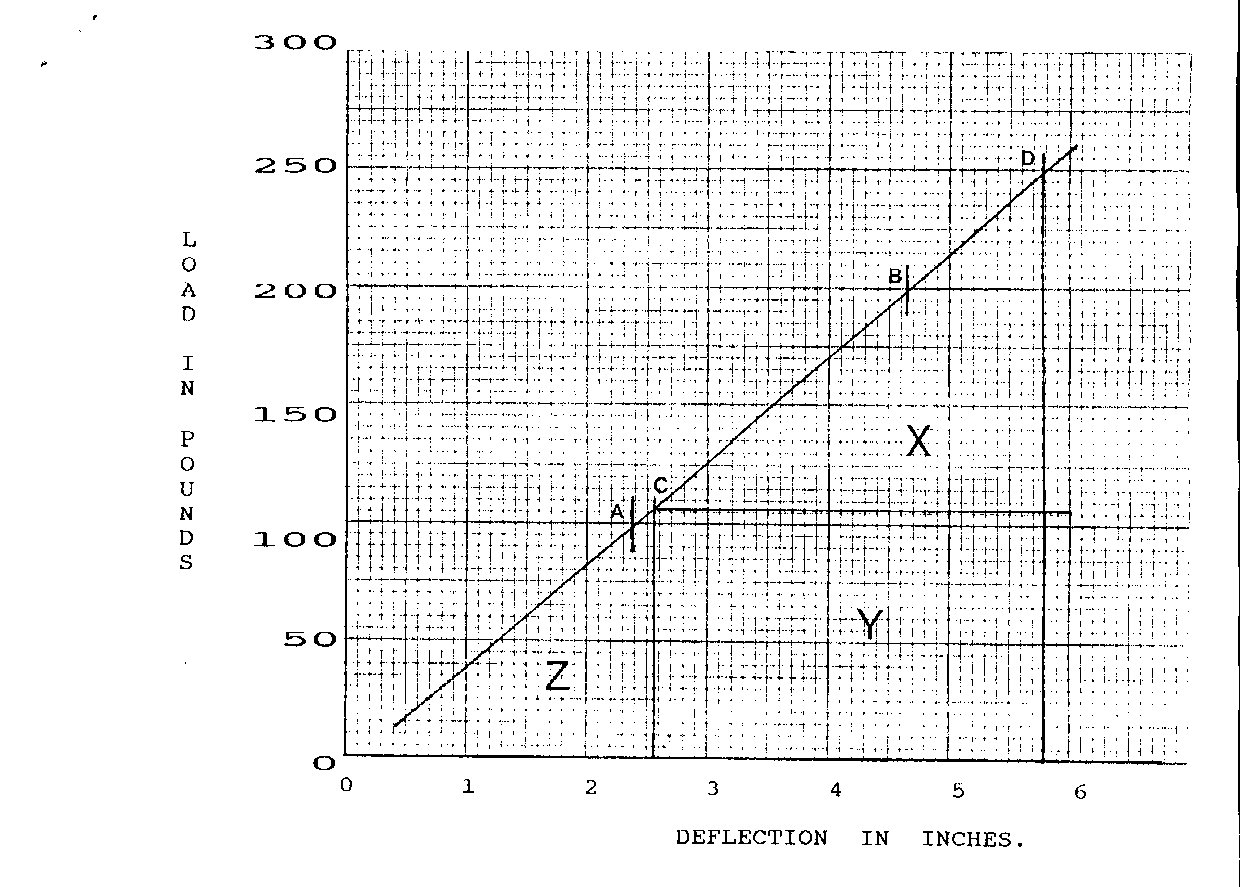
Round Wire Spring | No 1. |
Weight | 5.3oz (168 grammes) |
Length before testing | 11.20" |
Length at test | 10.85" |
Total number of turns | 33 |
Dimension of material | 0.142" diameter round wire |
Cross sectional area of material | 0.0158 square inch |
Length at 100 lbs load | 8.46" |
Length at 200 lbs load | 6.20" |
Length fully compressed | 4.82" |
Length in uncocked gun | 8.31" |
Length in cocked gun | 5.06" |
Initial compression | 2.50" |
Piston stroke | 3.25" |
Stored energy | 48.61 ftlbs |
48.61 Foot Pounds
WHEN FITTED TO AN HW 80.
CALCULATION OF ESC OF ROUND SPRING.
Free length minus length at 100 Lbs. load gives Point A. 10.85” - 8.46” = 2.39” deflection.
Free length minus length at 200 Lbs. load gives Point B. 10.85” - 6.20” = 4.65” deflection.
Free length minus uncocked length gives initial compression Point C. 10.85” - 8.31” = 2.54”
The initial compression plus the piston stroke gives the total compression. Point D. 2.54” + 3.25” = 5.79”
Area of section Y = Piston stroke multiplied by the load. 3.25” x 107 Lbs. = 347.75 Inch pounds.
Area of section X = Piston stroke multiplied by half the load. 3.25” x 72.5 Lbs. = 235.62 Inch Pounds.
347.75 + 235.62 Inch pounds divided by twelve gives 48.61
Ft . Lbs.
|
|
273 page 13
Square Section Spring | No 2. |
Weight | 6.44oz (182.5 grammes) |
Length before testing | 9.375" |
Length at test | 9.3" |
Total number of turns | 31 |
Dimension of material | 0.140" x 0.140" |
Cross sectional area of material | 0.0196 square inch |
Length at 100 lbs load | 7.62" |
Length at 200 lbs load | 6.08" |
Length fully compressed | 4.63" |
Length in uncocked gun | 8.31" |
Length in cocked gun | 5.06" |
Initial compression | 0.99" |
Piston stroke | 3.25" |
Stored energy | 43.6 ftlbs |
43.6 Foot Pounds
WHEN FITTED TO AN HW 80
CALCULATION OF ESC OF SQUARE SPRING.
Free length minus length at 100 Lbs. load gives Point A. 9.3” - 7.62” = 1.68” deflection.
Free length minus length at 200 Lbs. load gives Point B. 9.3” - 6.08” = 3.22” deflection.
Draw a line through these two points.
Free length minus uncocked length gives initial compression Point C. 9.3” - 8.31” = 0.99”
The initial compression plus the piston stroke gives the total compression. Point D. 0.99” + 3.25” 4.24”
Area of section Y = Piston stroke multiplied by the load. 3.25” x 55 Lbs. = 178.75 Inch Pounds.
Area of section X = Piston stroke multiplied by half the load. 3.25” x 106 Lbs. = 344.5 Inch Pounds.
178.75 + 344.5 Inch pounds divided by twelve qives 43.6 Ft.Lbs
|
|
 |
e-mail: webmaster(at)jonger(dot)co(dot)uk